The new tubas and Euphoniums will be on display at the Army Tuba Conference January 27-30. http://www.usarmyband.com/tuba/tubaeuphonium_conference.html
I will be at the NAMM show in Anaheim with the J-700 tuba and I-800 Euphonium. Unfortunately I will not have the Weingrill tubas and Euphs but I will have them at the Army show. Plans are to have the Nirschl J-880 CC tuba at that show as well.
Then plans are to take the whole dog and pony show to TMEA in San Antonio February 10-13. I will be in Texas the week following TMEA for special appointments showing the instruments.
I have posted the new professional pictures of the aforementioned instruments on the apporpriate links at the right.
Wednesday, December 30, 2009
Tuesday, December 22, 2009
Midwest Convention
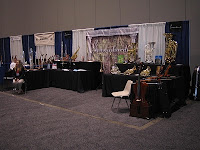.jpg)
Midwest Band and Orchestra Convention 2009 was in McCormick place for the first time.
I, for one, like the new venue. Lots of room; high ceiling/we can talk while people are playing.
Thanks to everyone who came by to look at new product. The French horns were a big hit. It's taken a while for the word to spread about the advantages of the 3/4 double but consensus is that it is great for beginners and a very good horn beyond the beginner stage. College players are always impressed with the D-88O big Kruspe-style nickel horn with all its extra features.
The J-700 4/4 BBb tuba was a big draw, thanks in part to Don Harry spreading the word. I will have it on display at NAMM, the Army Conference in DC and at TMEA. Some dealers have it in stock already, Buckeye Brass, Rieman Music and Griggs Music among them.
The CC tuba and the new Weingrill rotor tuba did not arrive in time but I will have both for the Army Conference Jan 27-30 at Ft Meyer. I will have the new Weingrill compensating Euphonium there as well. It is a totally new design.
I posted some pictures from Midwest on the link at the right.
Saturday, September 26, 2009
J-700 Demo Trip
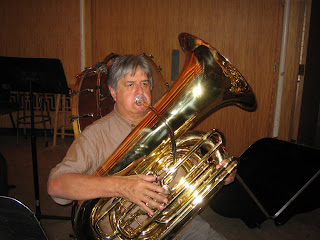
On my September trip I stopped at the Buffalo Philharmonic hall where Don Harry, the principal tubist and also tuba prof at the Eastman School of Music tried the new production run J-700LQ on stage. Also there were tubists T.J. Ricer and Mark Jones. All where impressed with the new tuba, both the sound, construction and features. Considering the playability and price Don said, "This may be the end of the road for all other BBb tubas." Don likes to play the right instrument for the music and likes a BBb tuba for many Russian pieces. This was something he learned from his teacher, the great Bill Bell.
All three players appreciated the cupro-nickel mouthpipe and the MTS case as well as the intonation and "sweet" sound.
Then it was on to Capital University in Columbus, OH. Tony Zilincik, tuba prof, echoed Don's praise of the J-700.
Tuesday, August 18, 2009
New W. Nirschl J-700 Tuba.
Walter is in Brazil this week inspecting the first production run of the J-700 tuba. If they pass inspection we should have our first batch in Elkhart no later than the end of September. MSRP (Manufacturers Suggested Retail Price)is set at $6,229 for lacquer and $7,069 for Silver.(See your W. Nirschl dealer for a quote or school bid.)
To see pictures of the proto-type in Walter's shop click the "Geretsried" link at the right. To see the J-700 compared to some historical tubas, click "York Lineage".
Thursday, April 2, 2009
Friday, March 27, 2009
Saturday, March 21, 2009
Band History 101
Introduction:
In my career I have had the great good fortune to have met, played for and learned from some legends and giants in the music industry. The Cleveland Orchestra’s Summer Home, Blossom Music Center has a concert band comprised of some orchestra members and other professionals from Northeast Ohio. I had the good fortune to
be a member of that band when Meredith Wilson was the Director. For those that don’t know, Meredith Wilson wrote, among other things, ‘The Music Man.’ He was also the piccolo player in the Sousa Band. Mr. Wilson was inspired to write ‘The Music Man’ partly by the life of Lynn Sams.
←MeredithWilson
Lynn Sams was a salesman for the Conn Corporation in the early 1900’s and a founding member of the American Bandmasters’ association. Although I never had the opportunity to meet Sams, I did know one of his contemporaries who also went from school to school
establishing bands and turning them over to a bandmaster he would hire. Charlie Gorby was one of these gentlemen. (http://www.lib.umd.edu/PAL/SCPA/ABA/Sams/Sams.html)
Football:
One of my students told me he had a great relationship with the football coach and in fact, the Music Boosters were given the concessions at football games by the coach. I asked how he had such a great relationship with the coach. He told me that when he started, he went to a football practice and sat in the bleachers. The coach came over and asked if he was a parent. When he said that he was the band director, the coach was surprised and asked why. “Well, we will be playing at all the games. I though I’d check out the team that I’ll be routing for.” They went out for coffee where the coach said the band was important to the morale of the team.
Did you ever ask the football coach to guest conduct? You know, one of those special marches.
Community Outreach:
Jacque Dillon, an industry legend and pioneer string teacher told me she had frequent requests to take ensembles out for performances in the community. Jackie said it is nice to play at nursing homes but her priorities were to “perform where the votes were.” She never turned down the luncheon requests at Rotary Club and the like.
North Allegheny High School has a huge string ensemble called ‘Strolling Strings’. They are frequent performers at Rotary and Kiwanis luncheons. The students stroll from table to table
with as few as 12 instrumentalists to as many as 200. Repertoire includes Pachelbel's "Canon in D," Tchaikovsky's "Sleeping Beauty Waltz," and Strauss's "Emperor Waltz," and folk medleys. Kiwannis members always support school levies and encourage their own students to play string instruments.
Soap Box:
Remember, there is strength in numbers. And job security too.
If you believe in what you’re doing, shouldn’t it be required of every student in the school?
Not that it will be, but what a great premise from which to start.
Who asks your students’ parents if the student will be continuing in band?????
The Music Store! It is a financial commitment.
Keep in mind the music store is your ally. They live and die with your success.
“Decades from now, no one will remember how many notes your first clarinet missed. No one will remember your rating at state contest. But how you influence your students will impact the quality of civilization for generations.” Apologies to Dr. Tim if I paraphrased.
Thank you all for what you do.
Richard Barth
Have stories to add?I invite you, the band director, to share additional stories that need to be shared with future generations. We tend to think our music programs are an entitlement. As we understand where they came from, we may learn some great tricks for keeping them going. Please keep stories to one short paragraph. Add a picture if you like. I’ll post as many as I can.
In my career I have had the great good fortune to have met, played for and learned from some legends and giants in the music industry. The Cleveland Orchestra’s Summer Home, Blossom Music Center has a concert band comprised of some orchestra members and other professionals from Northeast Ohio. I had the good fortune to
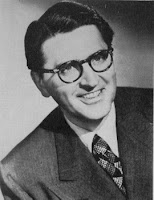
←MeredithWilson
Lynn Sams was a salesman for the Conn Corporation in the early 1900’s and a founding member of the American Bandmasters’ association. Although I never had the opportunity to meet Sams, I did know one of his contemporaries who also went from school to school
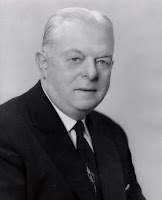
←Lynn Sams
Free Sousaphone:Charlie Gorby told me he could get parents to buy flutes, clarinets, trumpets and
trombones. But when it came to the bigger instruments, he turned to the local Kiwannis Club. After getting the Club to purchase a new Sousaphone, Charlie assembled the band on the football field at half time. The Sousaphone player marched on with no instrument. An announcement was made that Kiwanis had a presentation. The president of the club carried out a Sousaphone and placed it on the shoulder of the Sousaphone player. Can you imagine the publicity for the club and the thrill for the president. Next year the club came to Charlie and asked “What can we buy for you this year?”

A tuba acquisition success story:
Alex Cauthen, tubist in the Dallas Wind Symphony used to teach high school. He knew that Marching Band was ‘the tail that wagged
the dog’ so when he needed a new concert tuba, he asked the principal for a ‘rehearsal
Sousaphone’ for the ‘off-season’.
Alex Cauthen, tubist in the Dallas Wind Symphony used to teach high school. He knew that Marching Band was ‘the tail that wagged
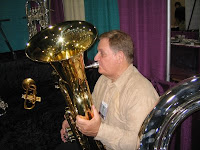
Sousaphone’ for the ‘off-season’.
Before there was a High School Band:
Another of the original Harold Hills I had the privilege to know was Charlie Holmes. One of his pet peeves was band directors who would not march in Summer parades or for Bond Issue parades. Charlie said, “These young directors do not understand that when I started schools did not have bands. We had orchestras to play classical music as part of the well-rounded education. It was not until I put a band on the football field at half time that I justified the existence of my band. Prior to that we had to rehearse after school.”
Tip:Don’t invite the administration to your concerts. Reserve the first row for them and the school board.
List their names in the program and tell them you will invite them to stand and be recognized right after intermission. (Remember board members are elected.)
Recruiting:
Doug McCullough took his Beavercreek High School band to Disney World. Doug also took a list of names and addresses of all the 4th graders. He had the seniors send post cards home about what a great time they were having at Disney World with the high school band. Next year his recruiting went through the roof.
(River City’s gonna have a boys’ band! Don’t know what that means? Watch the ‘Music Man’. I like the old one the best.)
Another of the original Harold Hills I had the privilege to know was Charlie Holmes. One of his pet peeves was band directors who would not march in Summer parades or for Bond Issue parades. Charlie said, “These young directors do not understand that when I started schools did not have bands. We had orchestras to play classical music as part of the well-rounded education. It was not until I put a band on the football field at half time that I justified the existence of my band. Prior to that we had to rehearse after school.”
Tip:Don’t invite the administration to your concerts. Reserve the first row for them and the school board.
List their names in the program and tell them you will invite them to stand and be recognized right after intermission. (Remember board members are elected.)
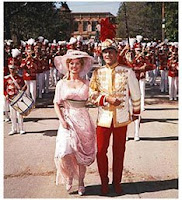
Doug McCullough took his Beavercreek High School band to Disney World. Doug also took a list of names and addresses of all the 4th graders. He had the seniors send post cards home about what a great time they were having at Disney World with the high school band. Next year his recruiting went through the roof.
(River City’s gonna have a boys’ band! Don’t know what that means? Watch the ‘Music Man’. I like the old one the best.)
Retention:
Close your eyes and think about the first time you were on stage.
Get your kids on stage after 8 weeks. No matter how simple the concert, a Christmas program for Grandma and Aunt Jane will go a long way to retention, both for the student and the parent.
Other Acquisitions:
In the 60’s, The Fifth Army Band did a recording of the music of Vincent Pershicetti. Rather than put his own picture on the record jacket, the director used pictures of Pershicetti and General Michaelis. General Michaelis was replaced by General Mock who wanted to see a record with his own picture on the jacket. The band director showed him a pile of recording equipment and said “We could do an even better recording if we had somewhere to install this equipment.” The next day the Army Corps of Engineers came to install a new studio.
Whose picture is on that new CD you just made?
Band Boosters:Many groups are called band parents. Are alumni and others in the community not welcomed? I know of one group that changed the name to band boosters, invited alums and senior citizen groups to join. (Board positions were limited only to parents). The extra membership dues bought two new piccolos and brought in a bigger audience from the senior center.
The Athletic Department:My wife and I served a two year stint as president of music boosters. We were told that athletics got all the money because the administrators were all jocks. I made a visit to the principal, the head of curriculum and the vice principal. In a non-confrontational meeting with each, I expressed that I represented 220 Music Boosters and we were grateful for the support that the Music Department had received and made a pitch for more. In casual conversation it turned out that the principal had played clarinet in his high school band, the vice principal had played trumpet in his college marching band and the head of curriculum, although he had no back ground in music himself, had two children in the choir.
Did you ever ask the principal to guest conduct? The president of the School Board? The mayor?
Close your eyes and think about the first time you were on stage.
Get your kids on stage after 8 weeks. No matter how simple the concert, a Christmas program for Grandma and Aunt Jane will go a long way to retention, both for the student and the parent.
Other Acquisitions:
In the 60’s, The Fifth Army Band did a recording of the music of Vincent Pershicetti. Rather than put his own picture on the record jacket, the director used pictures of Pershicetti and General Michaelis. General Michaelis was replaced by General Mock who wanted to see a record with his own picture on the jacket. The band director showed him a pile of recording equipment and said “We could do an even better recording if we had somewhere to install this equipment.” The next day the Army Corps of Engineers came to install a new studio.
Whose picture is on that new CD you just made?
Band Boosters:Many groups are called band parents. Are alumni and others in the community not welcomed? I know of one group that changed the name to band boosters, invited alums and senior citizen groups to join. (Board positions were limited only to parents). The extra membership dues bought two new piccolos and brought in a bigger audience from the senior center.
The Athletic Department:My wife and I served a two year stint as president of music boosters. We were told that athletics got all the money because the administrators were all jocks. I made a visit to the principal, the head of curriculum and the vice principal. In a non-confrontational meeting with each, I expressed that I represented 220 Music Boosters and we were grateful for the support that the Music Department had received and made a pitch for more. In casual conversation it turned out that the principal had played clarinet in his high school band, the vice principal had played trumpet in his college marching band and the head of curriculum, although he had no back ground in music himself, had two children in the choir.
Did you ever ask the principal to guest conduct? The president of the School Board? The mayor?
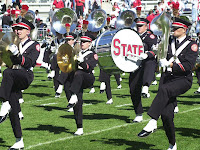
One of my students told me he had a great relationship with the football coach and in fact, the Music Boosters were given the concessions at football games by the coach. I asked how he had such a great relationship with the coach. He told me that when he started, he went to a football practice and sat in the bleachers. The coach came over and asked if he was a parent. When he said that he was the band director, the coach was surprised and asked why. “Well, we will be playing at all the games. I though I’d check out the team that I’ll be routing for.” They went out for coffee where the coach said the band was important to the morale of the team.
Did you ever ask the football coach to guest conduct? You know, one of those special marches.
Community Outreach:
Jacque Dillon, an industry legend and pioneer string teacher told me she had frequent requests to take ensembles out for performances in the community. Jackie said it is nice to play at nursing homes but her priorities were to “perform where the votes were.” She never turned down the luncheon requests at Rotary Club and the like.
North Allegheny High School has a huge string ensemble called ‘Strolling Strings’. They are frequent performers at Rotary and Kiwanis luncheons. The students stroll from table to table
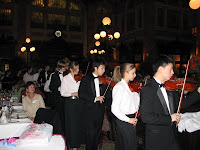
Soap Box:
Remember, there is strength in numbers. And job security too.
If you believe in what you’re doing, shouldn’t it be required of every student in the school?
Not that it will be, but what a great premise from which to start.
Who asks your students’ parents if the student will be continuing in band?????
The Music Store! It is a financial commitment.
Keep in mind the music store is your ally. They live and die with your success.
“Decades from now, no one will remember how many notes your first clarinet missed. No one will remember your rating at state contest. But how you influence your students will impact the quality of civilization for generations.” Apologies to Dr. Tim if I paraphrased.
Thank you all for what you do.
Richard Barth
Have stories to add?I invite you, the band director, to share additional stories that need to be shared with future generations. We tend to think our music programs are an entitlement. As we understand where they came from, we may learn some great tricks for keeping them going. Please keep stories to one short paragraph. Add a picture if you like. I’ll post as many as I can.
Friday, March 13, 2009
TMEA
Horn Maintenance
Brass Instrument Basic Care and Maintenance: French Horn(See separate page on re-stringing)DO NOT…Do NOT, if a valve is stuck, push on the lever. You will bend a lever or break a stem. French horn rotors are prone to ‘freeze up’ if left unused or if not well oiled. Grasp the stop arm around the center spindle and move it with your hand. If this doesn’t work, proceed to “un-sticking a valve” below.Do NOT boil your instrument or immerse it in hot water. It is important to wash your instrument periodically. Ignore web sites that suggest that instruments do not need to be cleaned. Germs can collect in the mouthpiece and mouthpipe. That said, do not over-react and boil the instruments. Do not put it in the dishwasher. Follow the steps below.Do NOT attempt to get a stuck mouthpiece loose with pliers or other devices not intended for this purpose. Pliers will harm the mouthpiece and when a mouthpiece cannot be dislodged with your own hand, chances are extremely high that you will twist or break the instrument itself with excessive force. Most music stores have a simple device called a mouthpiece puller made for the occasional stuck mouthpiece. Get thee to a music store. If you purchased or rented the instrument from the store they will pull the mouthpiece for a very nominal fee or perhaps no charge. They would much rather pull the mouthpiece as a service than have to cope with a damaged instrument.In the future, do not ‘pop’ the mouthpiece to put it in. Do insert with a slight gentle twist in one direction and extract with a twist in the opposite direction. (Most mouthpieces get stuck when the instrument is dropped. On rare occasion a mouthpiece gets stuck when the player tries to extract it by twisting aggressively in the same direction he used to insert it.)Do NOT wash the instrument with anything abrasive. Lacquered (D-500LQ, D-700LQ, and D-800LQ) have what is essentially a clear paint job protecting them from tarnish. Do not use any polish on lacquer. A soft cloth like old pajamas will usually do a superb job of wiping off finger prints. A glass cleaner like Windex can be used if necessary. Even a little valve oil on a cloth can be used for stubborn spots. The lacquer will last a lifetime if you wash your hands before handling the instrument and wipe finger prints off before putting the instrument away.Unlacquered instruments (D-780UL and D-880UL) can be polished with commercially available brass polish like BrassoTM.Mouthpieces are silver plated and can be polished with silver polish but toothpaste does a great job and is very safe. Once a month is plenty except during cold a flu season. An alcohol swab or mouthwash will not harm the mouthpiece. There is a brush made especially for the inside bore of the mouthpiece. See below. An electric razor brush also works but get one dad is done with.Do NOT remove any parts without securing them in a safe place. Piston valves need to be removed to be cleaned. But if they roll off the kitchen counter and land on the tile floor, the resultant dent may render them inoperable. Get a small box to put them in. I like to place them in a box laying at an angle with the valve stem on the side of the box. This way they do not roll around but they also do not pick up any dirt or lint.Likewise slides need a secure place if removed. Do NOT use petroleum jelly (VaselineTM) to lubricate slides. It has many useful purposes but lubricating brass slides is not one of them. Your music store has many fine inexpensive slide greases. They are a good investment. (Having a stuck slide professionally pulled costs more than the grease.) There are many lubricants on the market made for other purposes that work well. If your teacher recommends one it is probably fine.The valve oil that came with your instrument will be all you need for the first month. Soon, however, it is wise to acquire some maintenance accessories. Your music store is a great source. They can show you how to use these. You already have some of these around the house.· Slide grease· A piece of absorbent (not polyester or synthetic), lint free cloth approximately 12” square. An old cotton handkerchief will do nicely. A piece of muslin from the fabric store is great.· A soft cloth for wiping finger prints off the outside of the instrument. Old pajamas or flannel from the fabric store, or an instrument polishing cloth from the music store.· Mouthpiece brush or electric razor ‘pipe-cleaner’ type brush.· Brass instrument bore brush specially made for French horn also known as a snake.· A small wooden or rawhide mallet.· A wooden dowel rod ca. ½” diameter and ca. 5” long.· French horn string. (Fishing line works well but it must be ‘braided’ and at least 50lb test. Depending on the brand and the braid, it may require 80lb test or more and newer thin lines may require special knots so as not to pull through the hole.) Knot this and cut to length in advance. Keep some in your case for emergencies.· A screwdriver that fits the rotor screws. A cheap screwdriver can be filed thin to fit and is better than a blade that is too narrow.· A quality rotor oil with a needle tip is not necessary but recommended for those that can use it responsibly.Recommended Maintenance:Weekly:1. Wash the mouthpiece with soap and water (or occasionally with toothpaste and water) at least once a week. This is for your own health. Use a mouthpiece brush or electric razor brush to clean the inside.2. Push all the slides all the way in. It is easy to forget to move these once the tuning is set, but grease can dry inside and ‘freeze’ the slides in place or crust at the end so that the slides cannot be pushed in all the way.3. Remove the tuning slide. Place it in a safe place. Wash the inside of the mouthpipe (the first tube long, bent tube on the horn that connects the mouthpiece to the tuning slide) with the flexible bore brush and soap and water. Rinse. Wipe the tuning slide free of grease with a paper towel. Wash it with the flexible bore brush. Re-grease and replace.Cleaning the mouthpipe is very important for several reasons:1.) Your health. This is where germs collect.2.) This is also where acids and salts collect. Soap neutralizes these. If not neutralized, brass deteriorization can occur.3.) Foreign substances can build up and after time restrict the air flow. (Brushing your teeth before playing is a good habit for the instrument and the player.)* It is a good idea to take everything apart, wash and re-grease once a year. This is also recommended initially if you are using a previously owned instrument. Follow all the instructions above but remove all four slides and immerse the body of what remains in luke warm soapy water. Rinse well. Wash and re-grease all the slides, oil the pistons etc.See the new horns from W. Nirschl at www.wnirschl.com
Wednesday, February 25, 2009
Stainless Steel
Brass Valve Material FAQ
Piston valves in modern brass instruments are made primarily of three materials, Monel metal with brass ports (un-plated), Nickel Plated Nickel Silver with brass ports (plated), or Stainless Steel with brass ports (un-plated).
What makes them good
Monel has 65% nickel in it. Nickel plate has 100% nickel on it. Stainless Steel has 18% chrome and 8% nickel in it.
Arguments for each can be made depending on criteria used. It is important to identify the criteria before making a claim as to which material is superior.
Wear
A claim is frequently made for Monel as superior to Nickel Plate claiming that Monel does not wear as much as Nickel Plate. All valves wear. If they did not they could not be honed and lapped to the fine tolerances needed. In truth, Monel does not “show” wear like Nickel Plate because there is no plating to wear off exposing the areas of wear. Typically when lapping a valve, lapping compound imbeds in the softer material (the brass casing) and cuts the harder material, the piston. Dirt, it could be argued, can act as a lapping compound. This would imply that whether Monel, Nickel Plate or Stainless Steel, valve wear is primarily on the piston itself. That does not mean there cannot be wear on the casings too. Nonetheless, what many people call wear is, in fact, simply visible wear as seen only on plated valves when the plating wears off. This is not the whole story. The primary factors in wear are cleanliness and lubrication.
Coefficient of Friction and Oil Retention Whether sliding friction or static friction, the ‘slipperiness’ of the piston is often cited as a criteria for superior valves. A case can be made that Nickel Plate is best when this is the main issue. However, the slipperiness of the material also implicates it as worst for oil retention. In fact chrome plated pistons (not currently popular) are even slipperier but must have pronounced cross hatching from lapping to retain oil. In practice, nickel plated valves are frequently not hand-lapped to the casing making them less tight and canceling any benefit from reduced friction. Additionally, Nickel Plated valves of necessity have nickel plating inside the ports which alters the acoustical properties. The arguments change in the presence of different lubricants.
Corrosion resistance and susceptibility to electrolytic reaction
Resistance to corrosion and susceptibility to electrolytic reaction with the valve casing can be a significant factor for players with highly acidic or saline body chemistry. Greenish or brown build-up is not uncommon on Monel valves. This is due to an electrolytic reaction between the piston and the casing. The discoloration is actually brass from the casing itself as it leaches on to the piston. Nickel plated valves and stainless steel valves are less susceptible to this reaction.
Other Considerations
Thermal expansion is not frequently considered when addressing the merits of valve material. Whether a piston expands at the same rate as the casing can be a factor especially in cold weather marching bands.
Although tensile strength is sometimes cited as a consideration, unless poking a nail into the piston or rough use when removed from the casing the instrument is contemplated, this is usually not an issue.
Comparing the options
While the chart below cannot be considered a formula for comparison, it does rank the materials on the specific criteria. E.g. If your criteria is coefficient of dry sliding friction, Nickel Plate is best. If your criteria are visible wear or flaking plating, Monel and Stainless are preferred over Nickel Plate. If preserving the acoustics of the continuous brass tube are the criteria, Monel and Stainless are preferable to any plating. Your needs may emphasize one criteria more heavily than another. If considering trouble-free performance, stainless steel has the edge. If taking all factors into consideration, Stainless Steel will serve best in most situations.
Piston valves in modern brass instruments are made primarily of three materials, Monel metal with brass ports (un-plated), Nickel Plated Nickel Silver with brass ports (plated), or Stainless Steel with brass ports (un-plated).
What makes them good
Monel has 65% nickel in it. Nickel plate has 100% nickel on it. Stainless Steel has 18% chrome and 8% nickel in it.
Arguments for each can be made depending on criteria used. It is important to identify the criteria before making a claim as to which material is superior.
Wear
A claim is frequently made for Monel as superior to Nickel Plate claiming that Monel does not wear as much as Nickel Plate. All valves wear. If they did not they could not be honed and lapped to the fine tolerances needed. In truth, Monel does not “show” wear like Nickel Plate because there is no plating to wear off exposing the areas of wear. Typically when lapping a valve, lapping compound imbeds in the softer material (the brass casing) and cuts the harder material, the piston. Dirt, it could be argued, can act as a lapping compound. This would imply that whether Monel, Nickel Plate or Stainless Steel, valve wear is primarily on the piston itself. That does not mean there cannot be wear on the casings too. Nonetheless, what many people call wear is, in fact, simply visible wear as seen only on plated valves when the plating wears off. This is not the whole story. The primary factors in wear are cleanliness and lubrication.
Coefficient of Friction and Oil Retention Whether sliding friction or static friction, the ‘slipperiness’ of the piston is often cited as a criteria for superior valves. A case can be made that Nickel Plate is best when this is the main issue. However, the slipperiness of the material also implicates it as worst for oil retention. In fact chrome plated pistons (not currently popular) are even slipperier but must have pronounced cross hatching from lapping to retain oil. In practice, nickel plated valves are frequently not hand-lapped to the casing making them less tight and canceling any benefit from reduced friction. Additionally, Nickel Plated valves of necessity have nickel plating inside the ports which alters the acoustical properties. The arguments change in the presence of different lubricants.
Corrosion resistance and susceptibility to electrolytic reaction
Resistance to corrosion and susceptibility to electrolytic reaction with the valve casing can be a significant factor for players with highly acidic or saline body chemistry. Greenish or brown build-up is not uncommon on Monel valves. This is due to an electrolytic reaction between the piston and the casing. The discoloration is actually brass from the casing itself as it leaches on to the piston. Nickel plated valves and stainless steel valves are less susceptible to this reaction.
Other Considerations
Thermal expansion is not frequently considered when addressing the merits of valve material. Whether a piston expands at the same rate as the casing can be a factor especially in cold weather marching bands.
Although tensile strength is sometimes cited as a consideration, unless poking a nail into the piston or rough use when removed from the casing the instrument is contemplated, this is usually not an issue.
Comparing the options
While the chart below cannot be considered a formula for comparison, it does rank the materials on the specific criteria. E.g. If your criteria is coefficient of dry sliding friction, Nickel Plate is best. If your criteria are visible wear or flaking plating, Monel and Stainless are preferred over Nickel Plate. If preserving the acoustics of the continuous brass tube are the criteria, Monel and Stainless are preferable to any plating. Your needs may emphasize one criteria more heavily than another. If considering trouble-free performance, stainless steel has the edge. If taking all factors into consideration, Stainless Steel will serve best in most situations.
How we test
When we test brass instrument tuning at W. Nirschl we play loud.
I have often heard the expression “Anyone can play loud. It takes talent to play soft.”
Not to deny that statement but having had the great fortune to perform as an extra with The Cleveland Orchestra and the Metropolitan Opera Orchestra, let me say that one reason a professional orchestra sounds as soft as it does in a pianissimo is because it is so very loud in a fortissimo. And the fortissimo is played with a good quality sound. It is partly the contrast that makes a pianissimo sound so soft.
So one reason to test loud is because it is a legitimate dynamic.
Another reason to test loud is because it is much more difficult to bend a pitch at fortissimo. It is much easier to bend a pitch at pianissimo. If a player is going to play with dynamic contrast, he must tune his instrument where it centers in a fortissimo and train himself to maintain that pitch as he makes a diminuendo.
Another technique I use in testing is to slur up to a note; look at the tuner; and then slur down to the not; look at the tuner. If a note has a wide ‘slot’ or wiggle room, it is likely to be lower when approached from above ad higher when approached from below. The wider the approach, the larger the difference is likely to be.
It is important to test softly for valve or slide action, noise etc. But for finding the center of the pitch, nothing compares to loud.
We also test the instruments with a mechanical device to find leaks. If an instrument leaks it is likely to negatively impact the extremes of range. Our brass technicians are accomplished brass players with average range. Although I have not played professionally for over 25 years (due to what is often referred to as focal dystonia) I have been blessed with the ability to play extremely high and low on all the brass instruments. I occasionally get called to the brass room to confirm the playability of an instrument. Those that don’t play, don’t get shipped.
Trombone slides are tested in playing position. I know of no better test of a trombone slide than to put it in playing position and let the slide fall. Playing position is a downward tilt of the slide of 11 to 25 degrees and the upper tube leaning clockwise 30 to 60 degrees from vertical. I know that some people test slides in a vertical position, some measure and I’m sure there are other tests as well. We use playing position because it is the only test that tests the bearing surfaces that are actually used in performance. We test dry and occasionally spot check with cream and water. We sometimes use Trombotine, sometimes slide-o-mix, sometimes rapid comfort and sometimes Brylcream. We know of players that use Pledge furniture polish and others who use Cold Cream or Dry Skin Cream. We do not use slide oil. I know that student instruments are routinely lubricated with oil as a logistical compromise. It does not work well. Manufacturers of student trombones have tried for many years to find an alternative. Some have even packaged a mixture of cream and water as an oil substitute. That mixture proves to be an even bigger problem because students do not clean the mixture off daily leaving it to ‘cake’ as it dries out.
Trombone players divide into camps or preferences when it comes to slide lubrication. But it is universally accepted that a cream of one type or another, combined with water spray continues to be state-of-the-art. See our article(video) on slide cleaning and lubrication.
I have often heard the expression “Anyone can play loud. It takes talent to play soft.”
Not to deny that statement but having had the great fortune to perform as an extra with The Cleveland Orchestra and the Metropolitan Opera Orchestra, let me say that one reason a professional orchestra sounds as soft as it does in a pianissimo is because it is so very loud in a fortissimo. And the fortissimo is played with a good quality sound. It is partly the contrast that makes a pianissimo sound so soft.
So one reason to test loud is because it is a legitimate dynamic.
Another reason to test loud is because it is much more difficult to bend a pitch at fortissimo. It is much easier to bend a pitch at pianissimo. If a player is going to play with dynamic contrast, he must tune his instrument where it centers in a fortissimo and train himself to maintain that pitch as he makes a diminuendo.
Another technique I use in testing is to slur up to a note; look at the tuner; and then slur down to the not; look at the tuner. If a note has a wide ‘slot’ or wiggle room, it is likely to be lower when approached from above ad higher when approached from below. The wider the approach, the larger the difference is likely to be.
It is important to test softly for valve or slide action, noise etc. But for finding the center of the pitch, nothing compares to loud.
We also test the instruments with a mechanical device to find leaks. If an instrument leaks it is likely to negatively impact the extremes of range. Our brass technicians are accomplished brass players with average range. Although I have not played professionally for over 25 years (due to what is often referred to as focal dystonia) I have been blessed with the ability to play extremely high and low on all the brass instruments. I occasionally get called to the brass room to confirm the playability of an instrument. Those that don’t play, don’t get shipped.
Trombone slides are tested in playing position. I know of no better test of a trombone slide than to put it in playing position and let the slide fall. Playing position is a downward tilt of the slide of 11 to 25 degrees and the upper tube leaning clockwise 30 to 60 degrees from vertical. I know that some people test slides in a vertical position, some measure and I’m sure there are other tests as well. We use playing position because it is the only test that tests the bearing surfaces that are actually used in performance. We test dry and occasionally spot check with cream and water. We sometimes use Trombotine, sometimes slide-o-mix, sometimes rapid comfort and sometimes Brylcream. We know of players that use Pledge furniture polish and others who use Cold Cream or Dry Skin Cream. We do not use slide oil. I know that student instruments are routinely lubricated with oil as a logistical compromise. It does not work well. Manufacturers of student trombones have tried for many years to find an alternative. Some have even packaged a mixture of cream and water as an oil substitute. That mixture proves to be an even bigger problem because students do not clean the mixture off daily leaving it to ‘cake’ as it dries out.
Trombone players divide into camps or preferences when it comes to slide lubrication. But it is universally accepted that a cream of one type or another, combined with water spray continues to be state-of-the-art. See our article(video) on slide cleaning and lubrication.
Subscribe to:
Posts (Atom)